
THE ARTEV™6000 IS A GAME CHANGER
In the global mining industry, there is a strong emphasis on adopting advanced technologies to maintain competitiveness.
Mining companies are publishing roadmaps around automation and decarbonation as a core value proposition for their investors and internal teams.
This trend is mirrored by global OEMs who are prioritising automation initiatives for haul trucks, drills and shovels.
With a plethora of asset choices forward-thinking mining managers can leverage a single chassis with diverse payload options to provide standardisation of asset selection for supporting mining operations.
This approach provides customers with increased visibility and enhanced control over autonomous operations fostering the harmonisation of battery charging infrastructure, simplifcation in maintenance and interoperability of an interchangeable payload systems.
These initiatives facilitate centralised coordination back to the control room that will become more complex as auxiliary mobile assets are required to be automated.
OUR STORY
In 2015, our founders identified that there was an environmental, safety and financial need to automate the delivery of explosives across the world.
By 2022, ongoing labour challenges and safety incidents associated with executing the drill and blast cycle plagued the industry. From operating near high walls, operating over uneven ground, cavities, hot ground, interactions between mobile equipment and people all combined to make this one of the key risks for leaders in mining.
Believing conventional methods were archaic, as they traditionally entailed personnel driving an MPU or stemming truck to deliver explosives or stemming, supported by a large auxiliary crew of operators and equipment. This conventional solution works relatively efficiently on flat benches however given irregular topography of some open pit mines, teams of individuals are often tasked with manually passing buckets along a human conveyor belt to access steep and challenging blast holes, elevating the risk of incidents associated with rock falls, open voids, muscular skeletal or general fatigue.
The founders of Jevons were driven by the ability to completely remove these risks from operations and developed and patented the ARTEV™6000 platform in 2023, configured for the drill and blast sector to solve this problem.
This innovative platform features a unique self-levelling chassis on grade technology, a vision system with automated hole detection capabilities, and software integration to streamline operations. These features not only optimise operation but also simplify the number of machines and personnel needed to operate in the explosives and stemming process.
By leveraging advanced vision and hole detection technology, the ARTEV™6000 vehicle can accurately position itself over blast holes, offering a comprehensive solution for deploying explosives and stemming material.
The vehicles payload agnostic feature facilitates seamless interchangeability of payloads on a single chassis, offering versatility beyond the conventional loading of bulk explosives and stemming material accommodating a range of alternative payloads including drilling fluids, de-watering equipment, sensors and monitoring equipment, geophysical sensors, even as a platform to manage the increasing number of electric cables in a pit as customers progress electrifying drills and shovels.
This approach provides customers with increased visibility and enhanced control over autonomous operations fostering the harmonisation of battery charging infrastructure, simplifcation in maintenance and interoperability of an interchangeable payload systems. These initiatives facilitate centralised coordination back to the control room that will become more complex as auxiliary mobile assets are required to be automated.
In March 2024, Jevons Robotics received the National CORE Innovation Hub's Hot 30 award, acknowledging their outstanding contributions to the industry. The ARTEV™6000 is presently deployed in the Pilbara region of Australia.
Jevons Robotics is currently in production with key players in the mining services sector including producing an ARTEV™1000 variant that will include the ability to deliver blast QA/QC activity within the quarry and construction segments, this will be available in 2025 and promises to bring the same safety and productivity improvements to this market.
Beyond mining, the company is exploring partnerships with agricultural, industrial, and defence sectors.
By addressing unmet needs that traditional equipment manufacturers may overlook, Jevons aims to provide specialised solutions tailored to diverse industry requirements.

Co-founders Todd Peate & David Crosbie
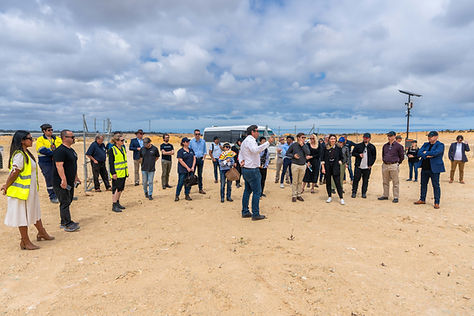
Customer presentation at the Australian Automation and Robotics Precinct
WHAT IS THE JEVONS PARADOX?
The Jevons paradox was first described by the English economist Willian Stanley Jevons in his 1865 book The Coal Question.
Jevons observed that England’s consumption of coal soared after the introduction of the Watt steam engine, which greatly improved the efficiency of the coal- fired steam engine.
Watt's innovations made coal a more cost-effective power source, leading to the increased use of the steam engine in a wide range of industries. This in turn increased total coal consumption, even as the amount of coal required for any particular application fell.
Jevons argued that improvements in fuel efficiency tend to increase (rather than decrease) fuel use, writing: "It is a confusion of ideas to suppose that the economical use of fuel is equivalent to diminished consumption.
"The very contrary is the truth”
At Jevons Robotics we firmly believe that by making Battery Electric and Autonomous machines more efficiently available to the market, adoption of these technologies for a safer and greener future will accelerate dramatically.
